The timely troubleshooting of DC motor faults in electric forklifts is crucial for the safe operation and efficiency improvement of electric forklifts and electric traction vehicles. In order to achieve the goal of quickly troubleshooting, one should have a grasp of the following situations of the motor: operating status; Usage, such as working environment, operating mode, load nature, power supply voltage, etc; Lubrication and operation of bearings, wear of components, ventilation, and air gap size between stator and rotor; The contact, cleanliness, and damage between each other, as well as the deformation, looseness, and damage of the rotor and stator cores. Three phase AC motor and DC motor are taken as examples to illustrate the common fault manifestations and maintenance methods of motor.
The faults of the DC motor of electric forklifts can be divided into two aspects: electrical and mechanical faults. Most electrical faults occur in the winding, commutator, and brush parts, while the mechanical parts mainly include the bearing parts. The common faults and diagnostic methods of DC motors are as follows:
1. The motor cannot rotate: ① The power supply is not energized or not connected; ② Poor contact between the brush and the commutator; ③ The brush and commutation are not connected (the brush ruler is too large); ④ There is a short circuit or grounding in the excitation winding of the electric winding; ⑤ The excitation winding wiring is incorrect, resulting in incorrect magnetic polarity; ⑥ The bearing is too tight to cause the armature to get stuck or be overloaded.
2. Sparks generated by the electric brush, severe friction between the commutator and the electric motor, and severe heating: ① The position of the electric brush is not correct; ② Poor electrical and exchange performance; ③ The brand and size of the electric brush are not appropriate; ④ The pressure of the brush spring is too low or too high; ⑤ The surface of the commutator is rough and uneven, with mica protruding between the commutator plates; ⑥ Armature winding, local short circuit or grounding fault; ⑦ Short circuit between commutator blades or commutator grounding.
3. The DC motor brush of an electric forklift emits abnormal noise: ① The brush spring pressure is too high; ② The brush texture is too hard; ③ Mica protrusion between the converter plates; ④ The brush size does not match.
4. Motor winding and iron core recession too high: ① Motor overload; ② The applied voltage is too high or too low; ③ There is a short circuit or grounding in the motor winding; ④ Poor ventilation and heat dissipation conditions; ⑤ The motor starts directly or reverses too frequently; ⑥ The stator, rotor, and iron core collide and the bearings are damaged.
5. Sparks or smoke inside the motor: ① Excessive spark under the brush; ② Short circuit or grounding of armature winding and winding; ③ The commutator lugs and the components of the armature coil are filled with electric powder and oil dirt, causing combustion; ④ Long term overload of the motor.
6. All copper plates of the DC motor of the electric forklift are blackened: the brush pressure is incorrect.
7. The reversing discs are grouped in a certain order and blackened: ① Short circuit between reversing discs; ② Short circuit of armature coil; ③ Poor welding or open circuit between the commutation plate and the armature coil.
8. The commutator plate turns black, but there are no certain rules: the center line of the commutator shifts or the surface of the commutator is uneven or out of circle.
-
Breakthrough improvements in bucket tines and masts"
Four-wheel drive off-road forklift installation bucket price shovel forklift truck with two vehicles
...Do you like ?0
Read more -
New energy forklift power system controller
The origins of forklifts can be traced back to 1917. After more than 100 years of development, forklifts, as the main mechanized loading and unloading, stacking and short-distance transportation tools, liberate people from heavy primitive human handling. Forklifts are widely used in factories, warehouses,...
Do you like ?0
Read more -
Electric forklifts vs. internal combustion forklifts
An electric forklift is a forklift that is powered by electric energy, usually using a battery as an energy source. A battery is a type of battery that is able to store a limited amount of electrical energy and release it when needed.
Do you like ?0
Read moreWhat are the daily maintenance of electric forklifts?
Electric forklifts are important equipment in warehousing...Do you like ?0
Read more"Electric Forklift Maintenance: Longer Life and More Efficiency"In view of the fact that many friends are still confused about the maintenance of electric forklifts, Xiaobian specially summarized the maintenance knowledge of electric forklifts<...
Do you like ?0
Read more"Level 3 maintenance is indispensable! Forklift maintenance strategy"First, the key points of the first-level maintenance of forklifts
...Do you like ?0
Read more
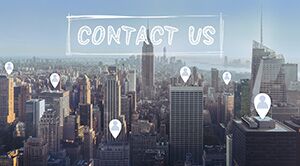
Technical Support: Magic Lamp